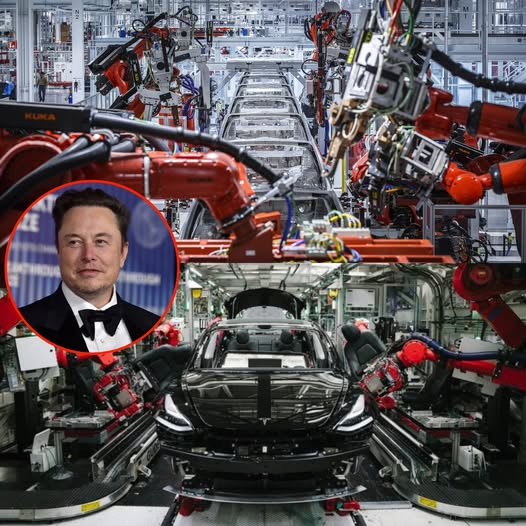
When Elon Musk first called Tesla’s future factories “alien dreadnoughts”, the world didn’t quite know what to make of it. The term conjured up visions of massive, sentient machines—extraterrestrial in appearance and capability—churning out vehicles with zero human involvement. It sounded like science fiction. But for Musk, it was a serious vision.
“We’re building the machine that builds the machine,” he once said. “And that machine should look like an alien dreadnought.”
At its core, Musk’s concept was radical: replace traditional assembly lines with fully automated, hyper-efficient factories, where robotic arms, AI-driven quality control systems, and modular automation work in seamless harmony. And while the road to that future has been anything but smooth, Tesla’s Gigafactories are steadily transforming the very nature of modern manufacturing.
The Growing Pains of Over-Automation
Tesla’s first major leap toward the alien dreadnought began at its Fremont Factory in California, especially during the production ramp-up of the Model 3 in 2017. In pursuit of unmatched efficiency, Musk pushed for aggressive automation, filling the facility with cutting-edge robots and complex conveyance systems.
But instead of speeding things up, automation bottlenecks slowed everything down. Robots struggled with tasks better suited for humans. Conveyor belts jammed. The lines became so complex that they were nearly impossible to debug in real time.
Musk later admitted:
“Excessive automation at Tesla was a mistake… Humans are underrated.”
That lesson led to a critical shift in Tesla’s strategy—not abandoning automation, but rebalancing it with human labor. Humans brought flexibility and problem-solving intuition that robots couldn’t match. The result? A smarter, more dynamic production process.
Shanghai: The Turning Point
The next big leap came in 2019 with the opening of Gigafactory Shanghai, Tesla’s first major plant outside the U.S. Unlike Fremont, Shanghai was built from the ground up with the right balance of automation and manpower.
It became a model for lean production:
- Robots handled repetitive tasks with precision.
- Human workers managed adaptability and maintenance.
- Machine learning systems monitored operations in real time.
The success was almost instant. Shanghai quickly became one of Tesla’s most productive and cost-efficient plants. Its lessons would pave the way for Musk’s next and most ambitious step.
Gigafactory Texas: The Near-Dreadnought
By 2025, Gigafactory Texas—also known as Giga Austin—emerged as the closest realization of Musk’s alien dreadnought vision. Sprawling over 2,500 acres and housing the world’s largest die casting machines (the “Giga Press”), the plant represents Tesla’s most advanced production concept yet.
Here’s what makes it special:
- Structural battery packs are integrated directly into the vehicle frame.
- The Cybertruck, with its stainless steel exoskeleton, is built using ultra-large, simplified assemblies.
- The factory floor uses real-time AI analytics to adjust production flow.
- Human input is minimal—robots dominate the floor, especially in high-volume tasks.
Giga Texas isn’t just a place that makes cars. It’s an ecosystem, a closed-loop where materials come in and finished vehicles roll out with stunning speed. It’s a manifestation of Musk’s belief that manufacturing innovation is just as critical as product innovation.
The Philosophy Behind the Dreadnought
What’s revolutionary isn’t just the robotics—it’s Musk’s philosophy. Most companies think of factories as back-end necessities. Musk treats them as front-line tech products in their own right.
He’s said repeatedly that “the factory is the product,” and Tesla’s manufacturing teams are encouraged to iterate on production design as aggressively as engineers iterate on vehicle design. That’s why Tesla is years ahead of competitors in terms of vertical integration, cost-efficiency, and production scale.
The Global Impact
Tesla’s factories are now benchmarks for the EV industry. Automakers from Volkswagen to BYD are studying Tesla’s gigafactories to understand how to scale EVs profitably.
Meanwhile, Musk isn’t stopping. Plans for Gigafactories in Mexico and India suggest that the alien dreadnought will continue to evolve, adapting to new markets and expanding Tesla’s reach.
If the ultimate goal is to make EVs affordable and accessible to all, then manufacturing breakthroughs—more than marketing or branding—will be the key to unlocking the future.
Dreadnoughts Are Real—And Here to Stay
What began as a quirky sci-fi metaphor is now materializing as the future of global industry. Elon Musk’s alien dreadnought may never fully eliminate the need for human workers, but it’s becoming a symbol of something just as powerful: a new way of thinking about how we build the world around us.
By 2025, Gigafactory Texas may be the first real glimpse of that future—a place where automation, intelligence, and ambition collide to redefine what a factory can be.